The Context
When Henry Ford introduced the concept of the assembly line, the landscape of manufacturing was forever changed. Invented in Britain, perfected in America and super-sized by the Soviet Union and China, the manufacturing process has shaped the course of the world economy for the past 2 centuries. Central to this was the need for efficient, real-time communication of plant floor status. In response, the Japanese pioneered the Andon system, a visual display to show status information on the plant floor. From simple lights that enabled operators to signal line status, Andon systems have evolved into sophisticated visual displays. A company specializing in production line control, entrusted Tismo with the development of a web based Andon System, for welding lines in automobile manufacturing.
The Problem
The web based Andon System was intended to monitor the status of various plant floor devices and robots on the assembly line, to increase the productivity of the process. It would also have to allow assembly line operators and workers to interact with maintenance personnel by pressing designated buttons. In addition to tracking the status of the plant floor, the Andon system would also have to allow the creation of users and shifts and monitor and report productivity.
The Solution
The team understood that a good factory should have minimal problems, should be able to quickly resolve problems, and should try to eliminate the root cause of the problems. Standardizing and accelerating the information flow would enable a fast response with minimum effort wasted on transmission. Keeping this in mind, the team proceeded to develop the Andon system.
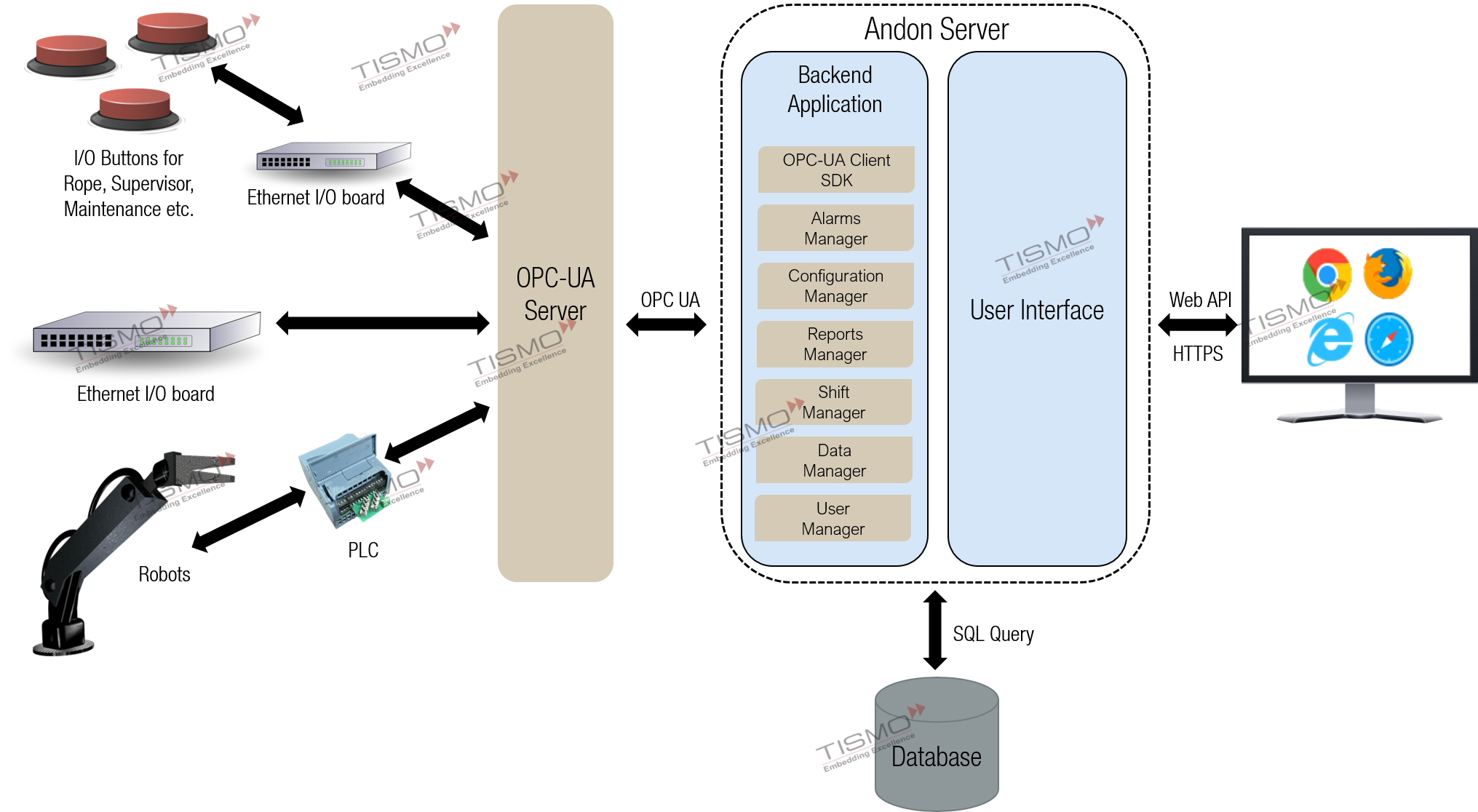
Architecture of web based Andon system
Tismo developed a web based Andon System to monitor the productivity of multiple lines in an automobile manufacturing plant. It was developed using C# on the ASP.NET Core framework and Angular was used to develop the user interface. Plant related data including I/O status, Events and Productivity data were stored in an SQLite database. The software allowed assembly line operators and workers to report issues and call supervisors or maintenance personnel, through OPC-UA enabled input-output (I/O) buttons. The issues were displayed as color coded icons, indicating the type of issue (supervisory/maintenance), location and status of resolution. Since it was a web app, the reported issues could be viewed on the Andon System displays on the plant floor (e.g. using a large Smart TV display) and on desktops in the cabins of supervisory and maintenance personnel, via Web APIs. The system also played different audio alarms, to alert the concerned personnel. Data was collected from various devices including PLCs, Ethernet I/Os etc. all connected through OPC-UA communication infrastructure, over a plant-wide Local Area Network (LAN).
Tismo employed an OPC-UA server to concentrate data from the I/Os, PLCs, and the Robots on the plant floor. A separate OPC-UA client application was developed to display this data, to be used along with the Andon System.
It supported the creation, editing and deletion of users, viewing and creation of shifts and shift types, and assembly line configurations. Additionally, it monitored the status of robots and generated reports on day to day productivity.
Summary
Tismo developed a web based Andon System using C# on the ASP.NET Core framework. Angular was used to develop the user interface. The software allowed assembly line operators and workers to report issues through OPC-UA enabled input-output (I/O) buttons. The issues were displayed as color coded icons on the Andon System displays on the plant floor and on desktops in the cabins of supervisory and maintenance personnel, via Web APIs. Data was collected from disparate devices including PLCs, Robots and Ethernet enabled I/Os using the OPC-UA communication infrastructure.
Cover Image: “Body/Frame Assembly Line” by Kojach is licensed under CC BY 2.0